About SiC
Silicon Carbide (SiC) is a hard covalently bonded material that consists of one silicon (Si) atom and four carbon (C) atoms. It is a non-oxide ceramic material. It is one of the most important advanced ceramic materials in use today. SiC occurs in different crystal structures called polytypes. There are over a hundred known polytypes of SiC, but only a few are commonly grown in reproducible form acceptable for use as semiconductors. The most common polytypes of SiC for electronics are 3C-SiC, 4H-SiC and 6H-SiC. Due to the differing arrangements of silicon and carbon atoms within the SiC crystal lattice, each SiC polytype exhibits unique electrical and optical properties.
Different SiC polytypes are composed of different stacking sequences of Si-C bilayers. A bilayer can be simplistically described as a planar sheet of silicon atoms coupled with a planar sheet of carbon atoms. The plane formed by a bilayer sheet of silicon and carbon atoms is called a basal plane. The stacking sequence of the 6H-SiC polytype requires six Si-C bilayers to define one unit cell that repeats in the crystallographic stacking direction.

Superior physical properties of SiC have made it a material of considerable interest to numerous industries, from aerospace to automotive, and from green energy generation to oil and gas extraction. SiC material properties include:
- 3X Wider Bandgap than Si – Higher energy required for electrons to transition from the valence band to the conduction band.
- Lower Intrinsic Carrier Concentrations than Si – Lower numbers of electrons in the conduction band limits undesired leakage current, making it an excellent insulator and granting its high temperature tolerance.
- 3X Higher Thermal Conductivity than Si – High rate of heat transfer through the material by conduction permitting efficient cooling to take place.
- Lower Coefficient of Thermal Expansion – Small volume change as temperature is increased.
- High Hardness – SiC is very hard with a Mohs hardness value of 9 (second only to diamond).
- High Resistance to Abrasion and Corrosion – Outstanding durability in adverse environments.
- Retains Elastic Resistance up to 1650°C – Suitable for high temperature industrial applications.
- Highly Radiation Stable – Although not immune to radiation degradation, SiC successfully survives intense neutron radiation and shows better radiation resistance than silicon.
- 10X Higher Critical Electric Field Strength than Si – Superior blocking voltage and enables faster power switching.
Manufacturing Challenges
Semiconductor devices require conductive signal paths and interconnects to be created to carry signals between devices on the same chip and to external circuit elements that reside off-chip. While SiC itself is capable of high-performance operation under extreme conditions, this ability is useless without contacts and interconnects that are also capable of operating under the same conditions. Constructing durable and reliable metal contacts and interconnects that operate at high temperature is one of the main challenges in manufacturing SiC semiconductor devices. Etching interconnects and signal paths on SiC is difficult because of its hardness and chemical inertness.
CoolCAD’s proprietary SiC etching process achieves etch depths that meet the reliability requirements of advanced high-power, high-temperature electronic devices that function in harsh environments.
SiC oxidizes at elevated temperature in an oxidizing atmosphere. Oxidation can be either active or passive. Active oxidation reduces the strength of SiC, whereas passive oxidation leads to the formation of a coherent silica (SiO2) layer that improves its performance in specific applications, such as in metal-oxide-semiconductor field-effect-transistors (MOSFETs). For this reason, understanding the oxidation behavior of SiC is an area of significant importance.
CoolCAD’s has expertise in all areas of SiC semiconductor device fabrication including the formation of metal interconnects and thin film dielectric layers.
Opportunities
SiC-based semiconductors are driving technological advances in numerous industries. Areas of application include:
Efficient Electrical Power Generation
SiC semiconductor devices have the potential of transforming today’s aging electricity power generation assets into an intelligent and sustainable power grid. The superior material properties of SiC high-power solid-state switches enable large efficiency gains to meet increased consumer electricity demands. Without building additional generation plants the quality and reliability of the power grid can be improved with SiC semiconductor technology.
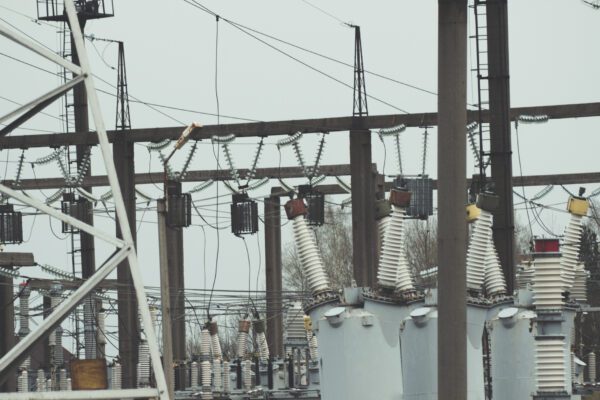
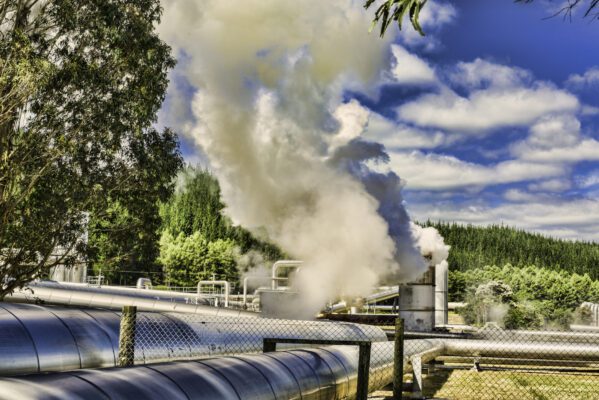
Geothermal Power Generation
Thermally stable wide bandgap semiconductor materials like SiC have the potential of transforming geothermal power generation through advanced sensor technology for the direct monitoring of geothermal reservoirs. SiC sensors survive supercritical geothermal environments, operating in H2O pressures up to 220 bar and temperatures as high as 374°C.
Electric Vehicles
SiC semiconductor devices are revolutionizing the way people move. From the wide-spread adoption of electric automobiles to evolution of mass transit vehicles such as buses and high-speed rail locomotives to electric power. SiC significantly improves the efficiency and speed of power generation compared to the conventional combustion engine while providing reliable and sustainable modes of transportation.

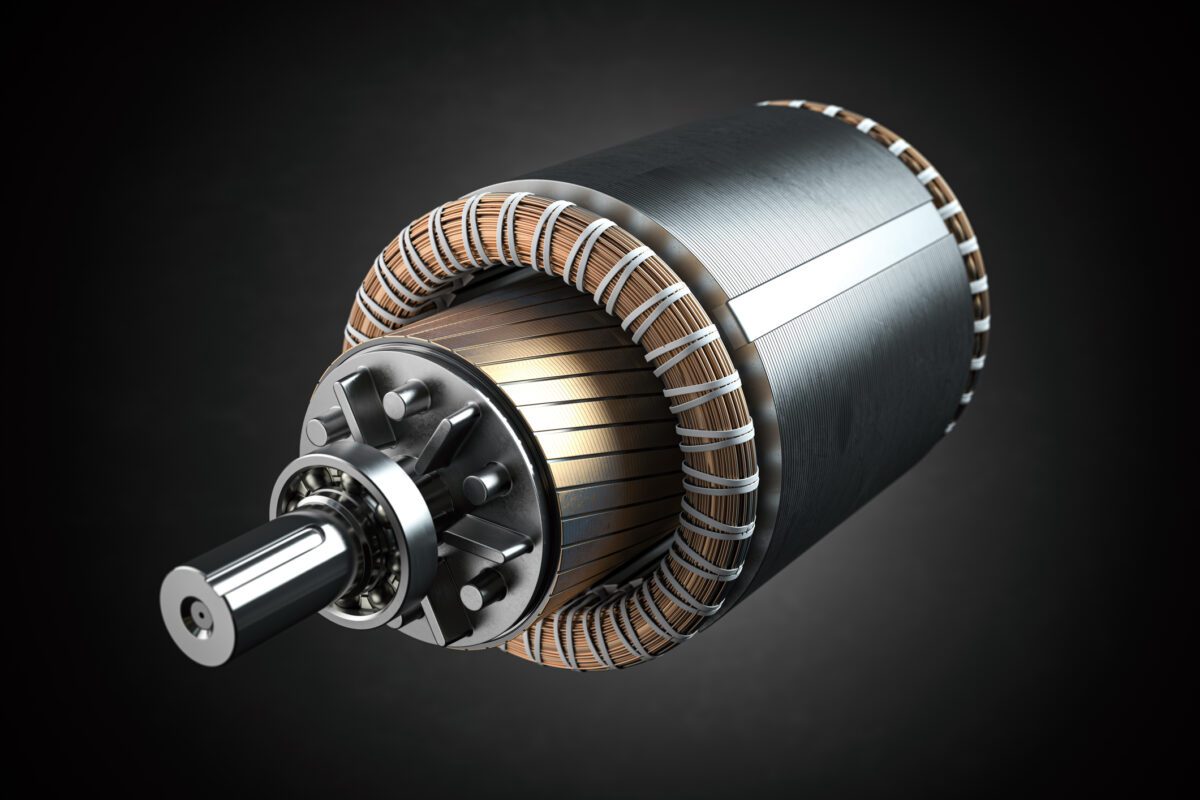
Converting Hydraulics & Pneumatics to Smart Electromechanical Controls
SiC semiconductor devices have the potential to replace hydraulic and pneumatic power systems with “smart” electromechanical controls and sensors that can operate in harsh industrial environments. Areas of application include robotics and industrial machinery.